Understanding the Process Behind Professional Packaging Machine Repair
Understanding the Process Behind Professional Packaging Machine Repair
Blog Article
The Ultimate Overview to Product Packaging Equipment Repair: Keep Your Workflow Running Efficiently
In the world of product packaging, the effectiveness of procedures hinges considerably on the dependability of equipment. Recognizing the details of packaging machine repair is important for keeping ideal performance and lessening disruptions. Normal maintenance not just expands the life of these devices however additionally addresses usual concerns that can hamper efficiency. As we check out the subtleties of troubleshooting and the essential decision-making procedure in between fixing and replacement, it becomes clear that a proactive approach can yield significant advantages. What certain methods can companies carry out to guarantee their product packaging procedures stay undisturbed?
Value of Routine Upkeep
Routine maintenance of product packaging makers is important for guaranteeing optimum performance and longevity. By implementing an organized maintenance timetable, operators can recognize prospective concerns before they escalate right into considerable problems. This positive approach not just minimizes downtime yet also expands the lifespan of the tools, ultimately bring about decreased functional costs.
Routine inspections permit the assessment of important components such as seals, belts, and sensors. Addressing deterioration without delay avoids unanticipated failings that could interrupt manufacturing and lead to expensive fixings. Additionally, routine upkeep aids ensure conformity with market criteria and guidelines, fostering a secure workplace.
Moreover, maintenance activities such as cleansing, calibration, and lubrication dramatically improve maker efficiency. Improved efficiency translates to consistent item top quality, which is crucial for keeping client fulfillment and brand credibility. A properly maintained product packaging device runs at optimal rates and minimizes material waste, contributing to total performance.
Common Packaging Maker Issues
Packaging machines, like any kind of intricate machinery, can encounter a selection of typical concerns that might impede their performance and performance - packaging machine repair. One common problem is irregular securing, which can cause item putridity and wastage if bundles are not correctly secured. This typically arises from misaligned components or used securing elements
Another regular issue is mechanical jams, which can happen as a result of foreign items, worn parts, or inappropriate placement. Jams can cause delays in manufacturing and boost downtime, inevitably impacting general productivity. In addition, electronic malfunctions, such as failure in sensors or control systems, can lead and disrupt procedures to inaccurate measurements or unpredictable machine habits.
Additionally, concerns with product feed can also develop, where things may not be provided to the packaging location constantly, triggering disruptions. Finally, wear and tear on belts and rollers can bring about suboptimal efficiency, needing instant interest to stop additional damages.
Understanding these typical concerns is important for preserving the integrity of packaging procedures, making sure that machinery runs smoothly and efficiently, which consequently helps in meeting manufacturing targets and keeping item top quality.
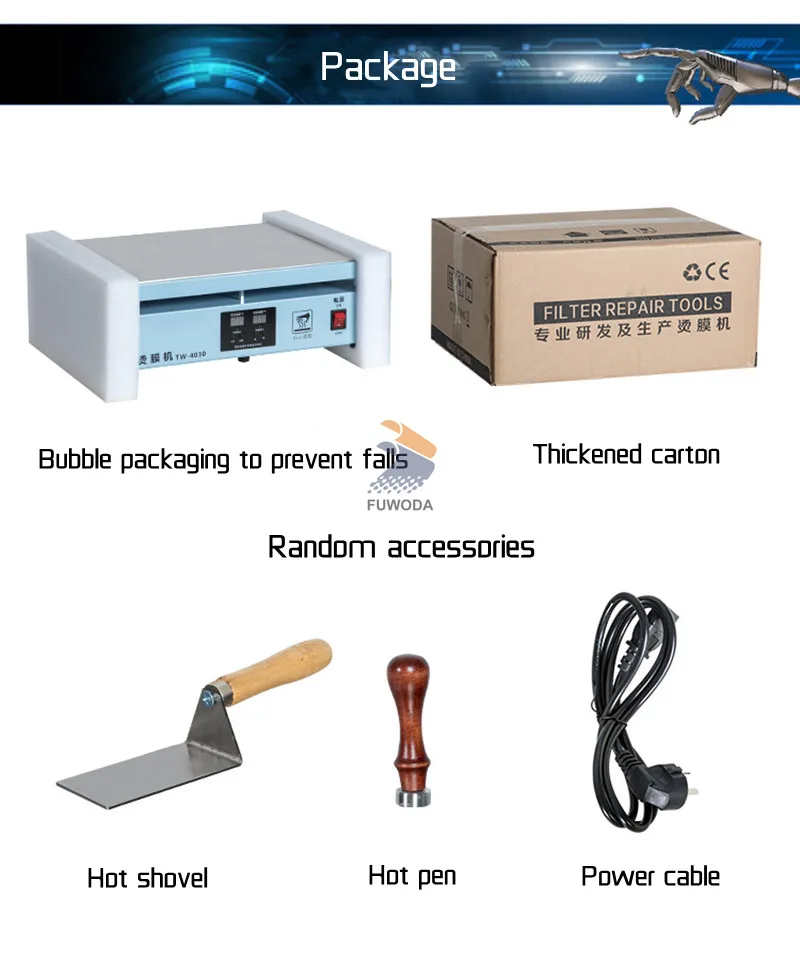
Troubleshooting Techniques
Effective troubleshooting techniques are crucial for immediately resolving issues that occur with product packaging makers. A systematic strategy is essential for recognizing the source of breakdowns and reducing downtime. Begin by collecting details concerning the signs and symptoms observed; this might consist of unusual noises, operational delays, or error codes shown on the maker's interface.
Following, refer to the equipment's guidebook for troubleshooting standards certain to the design concerned. This resource can give beneficial understandings right into typical concerns and suggested analysis steps. Make use of visual examinations to inspect for loosened connections, worn belts, or misaligned components, as check these physical factors usually contribute to functional failings.
Execute a procedure of elimination by testing specific machine functions. If a seal is not developing appropriately, assess the securing mechanism and temperature setups to establish if they meet operational specs. Record each step taken and the results observed, as this can help in future fixing initiatives.
Fixing vs. Replacement Decisions
When encountered with equipment breakdowns, deciding whether to change a product packaging or repair maker can be a complicated and vital option. This decision hinges on several crucial elements, including the age of the machine, the degree of the damage, and the forecasted effect on operational performance.
First of all, consider the device's age. Older makers may need even more regular fixings, leading to higher advancing prices that can surpass the financial investment in a brand-new unit.
Operational downtime is one more essential factor to consider. If repairing the device will certainly trigger long term hold-ups, investing in a new device that uses improved effectiveness and integrity could be extra prudent. Consider the schedule of parts; if replacement components are hard to come by, it may be a lot more strategic to change the equipment totally.
Eventually, performing a cost-benefit analysis that consists of both lasting and prompt effects will help in making an informed choice that aligns with your financial restraints and functional objectives. (packaging machine repair)
Preventive Procedures for Long Life
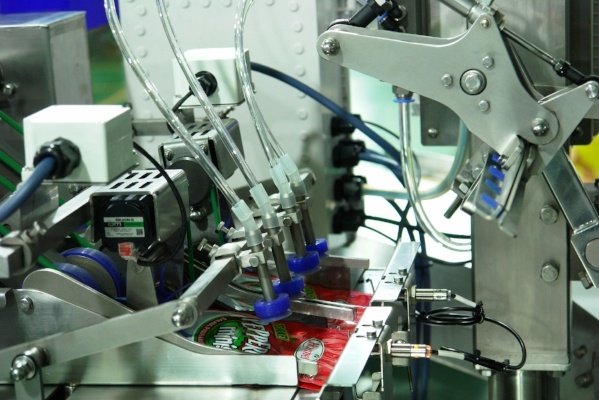
Secret preventative actions consist of routine lubrication of moving components, read review placement checks, and calibration of sensors and controls. Developing a cleansing timetable to remove debris and pollutants from equipment can significantly decrease wear and tear (packaging machine repair). Furthermore, keeping an eye on functional criteria such as temperature level and vibration can help discover abnormalities beforehand
Educating team to identify indicators of wear or breakdown is an additional crucial element of preventative upkeep. Encouraging drivers with the expertise to execute standard troubleshooting can bring about quicker resolutions and minimize functional disturbances.
Documents of upkeep tasks, consisting of solution records and assessment searchings for, cultivates responsibility and assists in notified decision-making relating to repair services and replacements. By focusing on safety nets, services can ensure their packaging equipments run at peak performance, ultimately leading to raised performance and minimized operational prices.
Verdict
In verdict, the effective upkeep and useful reference fixing of packaging makers are paramount for sustaining functional performance. By carrying out preventive procedures, organizations can enhance device long life and ensure continuous efficiency in product packaging procedures.
Understanding the complexities of product packaging equipment fixing is essential for preserving ideal performance and lessening disturbances.Regular maintenance of packaging devices is important for making sure optimum efficiency and long life.Product packaging machines, like any complex machinery, can encounter a variety of usual problems that may impede their efficiency and effectiveness. If repairing the equipment will certainly cause prolonged delays, investing in a brand-new equipment that supplies boosted effectiveness and dependability may be a lot more prudent.In conclusion, the effective maintenance and fixing of product packaging equipments are vital for sustaining operational performance.
Report this page